The organic matter of coke contains 5.97-5.96% carbon, 5-8% hydrogen, 3-4% oxygen and a small amount of sulfur and nitrogen. When the coke is heated to 85 degrees Celsius or more, the volatile substances are removed from it. The removal of volatile substances in Secondary heating is due to the breakdown of hydrocarbons in the coke. The more uniform the heating flow in the coking oven and the higher the temperature of the coke before the coking exit, the lower the percentage of volatile substances in it. Metallurgical coke usually contains 0.9 to 1.1% volatile matter. The reason for the moisture in the coke after quenching The most important reason for the presence of moisture in coke after turning it off is the entry of water into the coke cavities. When coke is stored in open space, coke quickly loses its moisture and its percentage decreases to 2.3 to 2.7 Therefore, the moisture percentage of coke depends on the method of quenching and also its surface per unit weight. The higher the ratio of surface to weight, the higher the moisture percentage. (If all other conditions are the same.) Therefore, the moisture percentage of fine coke It is 3-4 times more than coke with large seeds
.
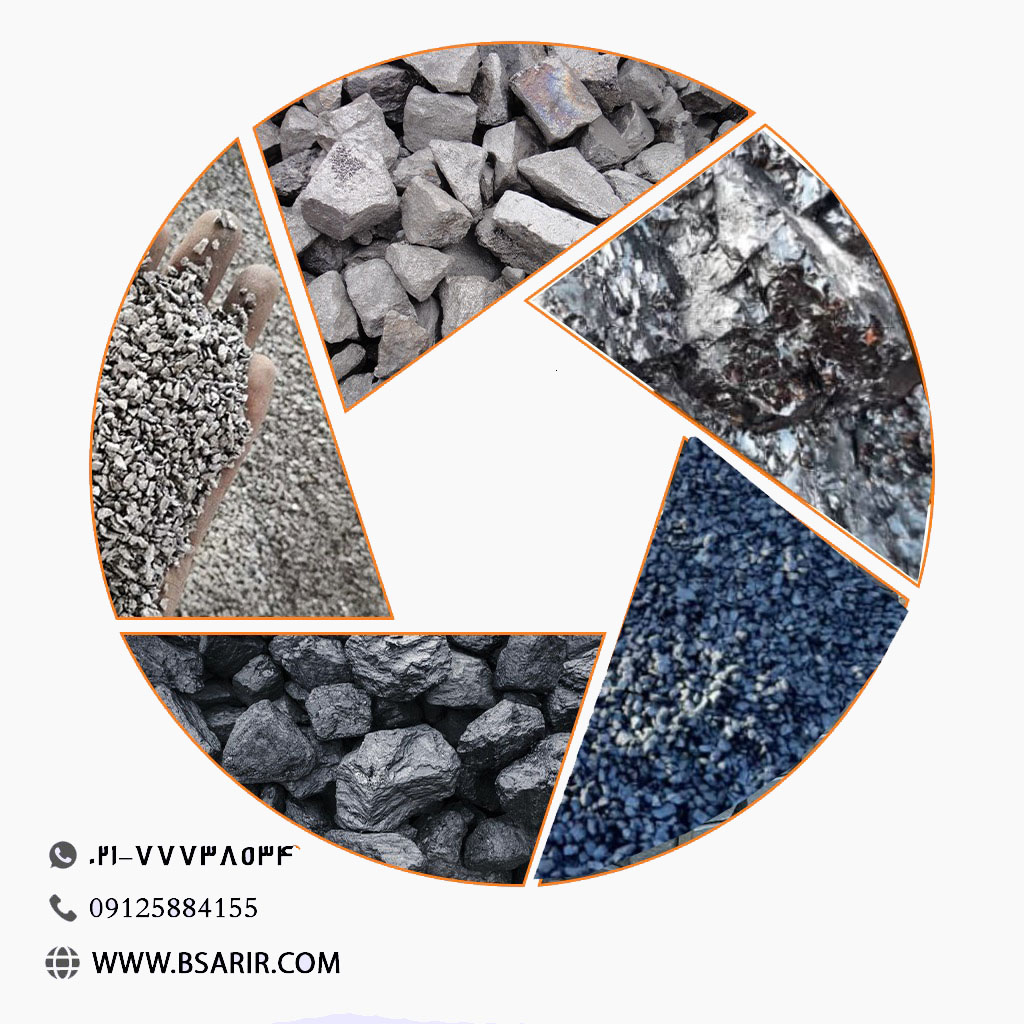
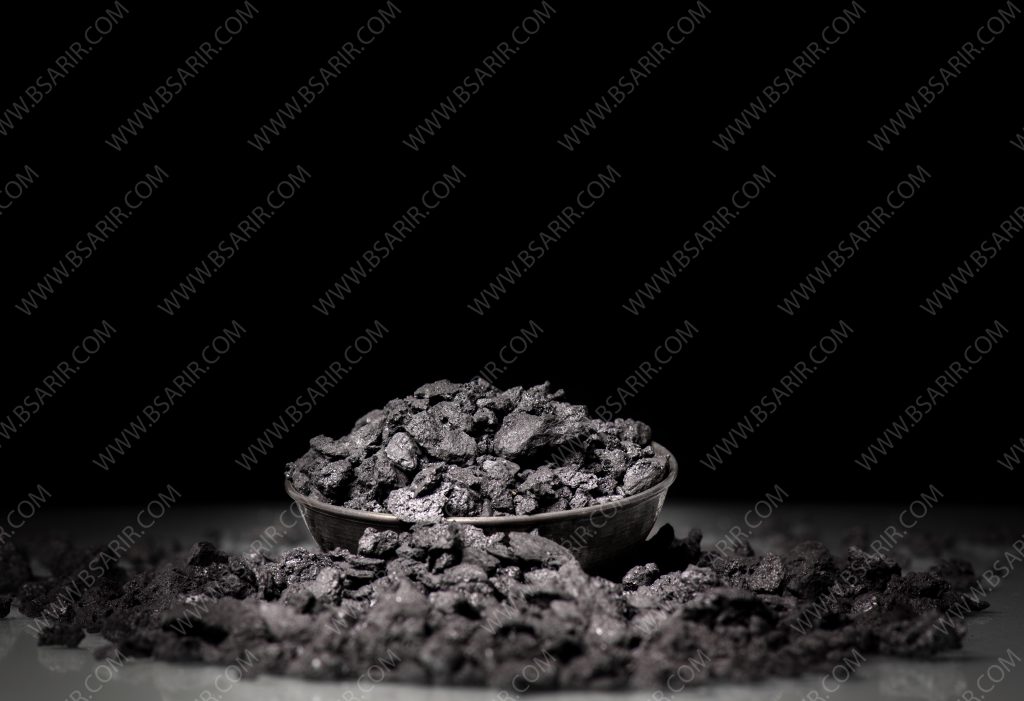
نظر مشتریان