Kok Metalurjisi
Kok, yakıt olarak kullanılan, çok yüksek karbonlu ve az miktarda safsızlık içeren bir maddedir.Kok, düşük küllü ve düşük kükürtlü bitümlü kömürlerden elde edilen karbonatlı katı bir maddedir.Kömürden elde edilen kok gri renkte ve aynı zamanda sert ve gözeneklidir.
Elbette kok da doğal olarak var ama en yaygın kullanılan kok, insanlar tarafından kömürden elde edilen koktur. Metalurjik kok üretmek için özel kömürler kullanılır ve kömürün özellikleri üretim kokunun özelliklerini belirler.Kömürün içindeki inorganik maddeler steril olarak adlandırılır ve kok içinde kül olarak kalır ve yüksek fırının performansını etkiler. yüksek fırında kok ve kireçtaşı tüketimini arttırır ve kok pillerinin üretim kapasitesini azaltır.
Kok Metalurjisi
Metalurjik kok, yüksek fırında kullanılan gözenekli bir malzemedir ve metalurji endüstrisinde kokun ana kullanımlarından biridir.Yüksek fırında kok, enerji sağlamada ve demir cevherlerini yenilemede ve yenilenen cevherin geçişi için gözeneklilik oluşturmada çeşitli roller oynar. gazlardır ve dökme demir karbürizasyonuna sahiptir.Kopel fırınlarında yakıt ve rejenerasyon maddesi olarak da kok kullanılır.Kokun döküm sanayinde de kullanıldığını belirtmek gerekir.
Kok, kükürt ve fosfor yüzdesine sahiptir.Sonuç olarak kok, kükürt ve fosforun çelik üretim prosesine girmesinde en önemli faktördür.Kükürt ve fosfor çelikteki zararlı elementlerdir.
Koklaştırma sürecini tanımak:
Demirin indirgenmesi için oksijeni demir oksitlerden ayıran bir maddeye ihtiyaç vardır.Bu maddeye indirgeyici madde denir.Tüm yüksek fırın reaksiyonları kok yakılması sonucu oluşan yüksek sıcaklıklarda gerçekleştirilir. fırınlarda kömürden elde edilen kok uzun süre kullanılmaktadır.Kok yerine az miktarda doğalgaz ve akaryakıt da kullanılmaktadır.
Canlandırma yeteneği
Doğal gaz hidrojenin rejenerasyon yeteneği kok karbonuna göre çok daha yüksektir.Bu nedenle yüksek fırında doğal gaz enjeksiyonu kullanılarak yüksek fırında yakılarak hidrojen gazı üretilmeye çalışılmaktadır.Günümüz modern fırınlarında Kömür yöntemi Kok tüketimini büyük ölçüde azaltan toz enjeksiyonu da kullanılmaktadır.
Kömür düşük mukavemetli ve yüksek safsızlık oranına sahip olduğundan (yaklaşık %35) yüksek fırın yakıtı olarak gerekli tüm şartları sağlayamaz, dolayısıyla gerekli koşullar sağlanıncaya kadar (yeterli mukavemet ve düşük safsızlık yüzdesi ve yüksek kalorifik değer) kok haline dönüşür. yüksek fırında şarj etmek için.
Kömürün kok haline dönüştürülmesiyle ortaya çıkan değişiklikler şunlardır:
1. Karbon yüzdesinin arttırılması ve dolayısıyla kalorifik değerin arttırılması.
2. Darbe, basınç, düşme ve aşınma gibi mekanik etkenlere karşı direncin arttırılması.
3. Kömür gazları ve uçucu maddelerin emisyonundan kaynaklanan uçucu safsızlıkların azaltılması
4. Kok gözenekliliğinin sağladığı daha fazla yanma için faydalı yüzey alanının arttırılması.
Kok, yüksek fırında gerekli termal enerjiyi sağlamanın yanı sıra demir cevherindeki demir oksitlerin rejenerasyonunu da gerçekleştirir.Rejenerasyon doğrudan karbon (yüksek fırın formlarının önünde) veya CO2, H2 gazı ile yapılabilir.
Kokanın fırın üzerindeki etkisi
Kokun kalorifik değeri maksimum, nem içeriği ise minimum olmalıdır. (Kokun nem içeriği söndürme kulelerinde kalış süresine ve koktaki su emme miktarına bağlıdır.) Kokun nem içeriğinin yüksek olması patlatma çalışmasını olumsuz etkiler. Çünkü yüksek fırında uygun ısıl durumun oluşmasını engeller, fırının verimini düşürür.
Şu anda İsfahan demir ergitmede kok söndürmek için ıslak yöntem veya sıcak kok üzerine soğuk su püskürtmek kullanılıyor ve kuru yöntem (inert gazla yani nitrojenle söndürme) kullanılmıyor. Nemi azaltmak mümkün. kok içeriğini arttırır ve mukavemetini arttırır ve elbette kok içerisine üflenen gazın enerjisinden de yararlanılabilir.
Bahsedilen durumlara göre uzun süreli kok için gerekli koşullar şunlardır:
1. Kalori değeri 4000 kcal/kg’dan az olmamalıdır.
2. Kükürt yüzdesi %1’den fazla olmamalıdır.
3. Kok yeterli güce sahip olmalıdır.
4. Kül oranı %14’ten az olmamalıdır.
5. Koktaki nem miktarı %9’dan az olmalı ve kok tanelerinin büyüklüğü 5-80 mm olmalıdır.Genellikle bir ton ham demiri eritmek için 450-500 kg kok gerekir ve bunun fiyatı kok miktarı %50-30’dur.Bir ton pik demirin fiyatıdır.
6. Uçucu madde oranı %1’den az olmalıdır.
Kok mukavemeti testi:
Koklaştırma ünitesinden üretilen kokun mukavemetini kontrol etmek için barban testi yapılır.Bu testte tane büyüklüğü 60 mm’den büyük olan 50 kg kok barban silindirine dökülür ve 4 dakika süreyle döndürülür. Dakikada 25 devirlik bir hız Daha sonra pireler dikenden çıkarılır ve 10 ve 40 mm’lik iğnelerden geçirilir (iğneler 40 mm veya 10 mm çapında dairesel deliklere sahiptir).
10. elekten geçen kok partiküllerini tartıp 50 kg cinsinden yüzdesini hesaplayıp M10, 40. elekten geçen kok partiküllerinin yüzdesini de M40 olarak raporlayınız.Kuvvetli kok M10’unun küçük olması uygundur. 6.8 ve M40’ı 80’in üzerinde.
Kok ve kimyasallar bölümü aşağıdaki üç ana bölümden oluşmaktadır:
1. Kömür sektörü
2. Kola bölümü
3. Kimyasallar Bölümü: Bu bölüm aşağıdaki beş alt bölümden oluşmaktadır:
4. Malzeme kurtarma bölümü
5. Asit kısmı
6. Benzol’ün Rafine Edilmesi
7. Biyokimya Enerji Bölümü
8. Kömür ve kok araştırma birimi
• Kömür sektörü:
Kömür bölümünün görevi kömürü kok hücrelerinde şarj edilmek üzere hazırlamak ve depolamaktır.Kömür madenlerden fabrikaya demiryolu ve kamyonla taşınır.Bu kömürler iç madenlerden temin edilir.Ayrıca kok hücrelerinde şarj edilen yaklaşık %40 Kömür, Avustralya’dan ithal edilmiştir.
one
Döner vagonun kömür bölümü bulunur.Kömür içeren vagonlar teker teker döner vagona girerek devrilir.Bunun sonucunda çevirme vagonu cihazının altında bulunan kömür bunkerlerine kömür dökülür.
two
Daha sonra kömür, bunkerlerin altında bulunan konveyör bantlar vasıtasıyla manyetik ayırıcıya eşit bir şekilde gider.Manyetik ayırıcıda, kömüre karışmış olması muhtemel metal parçalar ayrıştırılır.
tree
Daha sonra kömür bir değirmenden geçerek iki sıra on üçlü ve iki sıra yedişerli olarak yerleştirilmiş kömür silolarının tepesine çıkar.Her bir kömür silosu yaklaşık 2500 ton kömür kapasitesine sahiptir. siloların sıcaklığı 60 santigrat dereceden fazla olmamalıdır.
Her madenin kömürleri ayrı silolarda şarj edilir.Daha sonra siloların altından belli bir miktar kömür alınarak altta ve 4 sıra silo boyunca yer alan konveyörlere düşer.Bu sayede farklı tipte kömürler belirli ağırlık yüzdeleri kaldırılır.Bu kömürler iki değirmende 0 ila 3 mm boyutuna kadar kırılır, daha sonra akülere giderken miksere girer ve aynı zamanda üzerine su serpilerek tortu oluşması engellenir. tozun daha fazla karıştırılmasının yanı sıra kömür için gerekli nem de sağlanır.
Kömür şarjının teknik koşulları aşağıdaki gibi seçilir:
2. Maksimum %9 nem.
3. Uçucu maddeler %25 ila 28.
4. Kükürt maksimum %1.
5. Parçacıklar 0 ila 3 mm %75 ila 77.
Burada kömür bölümünün görevi sona erer ve her türlü kömür türünden yeterli neme, uygun boyutlara ve uygun yüzdelere sahip hazır kömür, kömür kulesine gönderilir.
Kola bölümü:
Bu bölümde kömür kulesinde bulunan hazır kömür, kok hücrelerinde bulunan şarj vagonu ile koklaşma periyodu olarak adlandırılan belirli bir süre içerisinde, uygun sıcaklık koşullarında (1100-1000 santigrat derece) şarj edilir. ve havanın yokluğu sırasında beş aşamada kok haline dönüşür.Bu aşamalar şunları içerir:
1. Kömür neminin 100 santigrat derece sıcaklıkta buharlaşması.
2. Hidrokarbonlar 350-300 santigrat derece sıcaklıkta salınır.
3. Kömür kütlesinin 350-480 santigrat derece sıcaklıkta macun haline getirilmesi.
4. Plastik kütlenin 480-550 santigrat derece sıcaklıkta yarı kok haline dönüştürülmesi aşaması.
5. Yarı kok kütlesini 480-1000 santigrat derece sıcaklıkta katı kok durumuna dönüştürme aşaması. Kok bataryasının girdi malzemesi kömür, çıkış malzemesi ise kok ve kok gazıdır.
Kok pili
Kok bataryası dikdörtgen küp şeklinde olup, enine duvarlarla hücre adı verilen daha küçük birimlere bölünmüştür.Bu hücrelerde kömür şarj edilir.Her hücre her iki tarafta kok gazının termal hücreleri tarafından arıtılır ve içlerinde yanar. ısıtılarak kömürün kok haline dönüştürülmesi için gerekli ısı sağlanır.Her hücrede kömürün şarjı ve boşaltımı üç adet şarj ve itme (boşaltma) makinesi ve kapı açıcılarla yapılır.
Regülatör
Kömürün yüklendiği hücrelere kok hücreleri, rafine kok gazının hava ile yandığı hücrelere ise termal hücreler denir.Termal hücrelerin sıcaklığı her zaman kontrol edilmelidir.Egzoz dumanının ısısını kullanmak ve önlemek için enerji kaybı Kok aküsünün altında bulunan gazlardan ve gelen havadan oluşan bir ısıtma sistemi kullanılır.Bu sisteme regülatör denir.
Yanma hücrelerinde dumanın çıkış yolu, merkezi yol değiştirme cihazı ve valfler tarafından gelen havanın yolu ile dönüşümlü olarak değiştirilmekte ve bunun sonucunda gelen havanın yanma için önceden ısıtılması sağlanmaktadır.
Koklaşma süresi bittikten sonra hücrenin iki yan kapısı kapı açıcı ve itici makineler tarafından açılır ve itici makine ile eriyik lokomotif arasındaki koordinasyon sağlandıktan sonra itici makinenin kolu dışarıdan kok hücresine girer. ve erimiş kok’u ileri doğru iter, bunun sonucunda kok hücrenin önünden alınır ve söndürme vagonuna dökülür.
Kok’un boyutlara göre sınıflandırılması
Söndürme vagonunun lokomotifi erimiş kokuyu söndürme kulesinin altına alır ve üzerine fenollü su püskürtülerek kok yaklaşık 90 ila 100 saniyede söndürülür ve ardından söndürme vagonu söndürme kulesinin altından dışarı çıkar ve kok dışarı atılır. Kok platformuna eşit şekilde düşer.Yaklaşık 20 dakika sonra kok, bir dizi taşıma bandı aracılığıyla kok granülasyon bölümüne gider, burada soğutulduktan sonra üç boyutta granüle edilir:
1. Aglomerasyon ve diğer kısımlarda yakıt olarak kullanılan 25 mm’den küçük kok taneleri.
2. Doğrudan yüksek fırına gönderilen 25-80 mm’lik kok taneleri.
3. 80 mm’den büyük kok taneleri granülasyon bölümünden alınarak kamyonla kok açık deposuna gönderilir ve tekrar kok granülasyon bölümüne girilerek filtrelenip kullanılır.Kopel tipi döküm fırınlarında da kok kullanılabilir.
Yüksek fırına ihtiyaç duyulmaması halinde, üretilen kok fazlası açık depolara aktarılmaktadır.
Kimyasal geri kazanım ve rafinasyon departmanı:
Kok gazı kok hücresinden çıktıktan sonra kimyasal geri kazanım bölümüne gönderilir.Bu bölümde farklı kimyasallar özel yöntemlerle kok gazından ayrıştırılır.Bu gazın kimyası.
Ortalama yoğunluğu metreküp başına 650 gram olan bir metreküp ham kok gazı aşağıdaki kimyasalları içerir:
1: Su buharı: 250-450 gram.
2: Katran buharı: 80-130 gram.
3: Amonyak: 82-120 gram.
4: Benzoil hidrokarbonlar: 32-34 gram.
5: Hidrojen sülfür: 2,8-5,6 gram.
6: Naftalin: 22-24 gram.
7: Hidrosiyanik asit: %1-8.
Kok bölümünden çıktıktan sonra üretilen ham kok gazı:
Koklaştırma prosesinden elde edilen ham kok gazı, kok bölümünden çıktıktan sonra, üzerine doğrudan amonyaklı su püskürtülerek önce sıcaklığı 700 ila yaklaşık 80 santigrat dereceye ulaşır.Bu sıcaklık düşüşü sonucunda katran ve suyun büyük bir kısmı, Amonyak ve naftalin, ince kok parçacıklarıyla birlikte ayrıştırılır.Daha sonra düşük sıcaklıktaki gaz, kok bölümündeki regülatörler vasıtasıyla iki emme makinesiyle separatöre (separatöre) gider ve amonyak suyu ve kalan katranı içeren ağır malzemeler Bir sonraki aşamada ise 8 adet soğutma kulesine giderek sıcaklığı 30 santigrat dereceye ulaşıyor.
Amonyum sülfat kısmı
Daha sonra bu gaz dolaylı su buharı ile 60 santigrat dereceye ulaşır ve daha sonra amonyum sülfat kısmına girer.Bu kısımda gaz sülfürik asit yüzeyinden geçtiğinde amonyum sülfat birikinti olarak çökelir.Bu birikintiler Kuruduktan sonra paketlenir ve tarımda gübre olarak kullanılır.Amonyum sülfat asit kısmından çıkan egzoz gazı benzol absorbsiyon kısmına gönderilir.
Benzen gazı üzerine dizel püskürtmek
Dizelin benzen gazı üzerine püskürtülmesiyle dizel emilir.Benzini emen dizel benzen rafinasyon bölümüne gönderilir.Bu rafinerinin ürünleri benzen, toluen, ksilen ve solventtir.Sülfürik asit gönderilir.Bu bileşiklerdeki kükürt Gazın içindeki ayrıştırılır ve daha sonra SO2’ye dönüştürülmek üzere yakılır.
Su buharı ve vanadyum pentoksit katalizörü enjekte edilerek SO3, H2SO4’e dönüştürülür. Ortaya çıkan sülfürik asit, amonyum sülfat kısmına gönderilir. Sülfürik asit kısmından çıkan gaz, fabrikanın gaz ağına girerek kok veya koklaştırmanın ısıtılmasında kullanılır. üretim hücreleri Buhar, enerji santrallerinde veya ön ısıtmalı haddeleme fırınlarında veya aglomerasyon pişirme makinelerinde kullanılabilir.
Kolanın kimyasal bileşimi:
Kokun organik maddesi %5,97-5,96 oranında karbon, %5-8 oranında hidrojen, %3-4 oranında oksijen ve az miktarda kükürt ve nitrojen içerir.
Kok 85 santigrat dereceye veya daha fazlasına ısıtıldığında uçucu maddeler açığa çıkar.
İkincil ısıtma kok içindeki hidrokarbonların parçalanmasından kaynaklanmaktadır.Koklaştırma fırınındaki ısıtma akışı ne kadar düzgün olursa ve kok çıkışından önce kok sıcaklığı ne kadar yüksek olursa, içindeki uçucu maddelerin yüzdesi o kadar düşük olur.Metalurjik kok genellikle içerir %0,9 ila 1,1 uçucu madde.
Söndürmeden sonra koktaki nemin nedeni
Kok kapatıldıktan sonra içindeki nemin en önemli nedeni, kok boşluklarına su girmesidir.Kok açık alanda depolandığında, kok nemini hızla kaybeder ve yüzdesi 2.3 ila 2.7’ye düşer. söndürme yöntemi ve birim ağırlık başına düşen seviyesi.Yüzey/ağırlık oranı ne kadar yüksek olursa nem yüzdesi de o kadar yüksek olur.(Diğer tüm koşullar aynıysa.) Dolayısıyla ince kokta nem yüzdesi 3-4’tür. büyük çekirdekli koladan kat daha fazla.
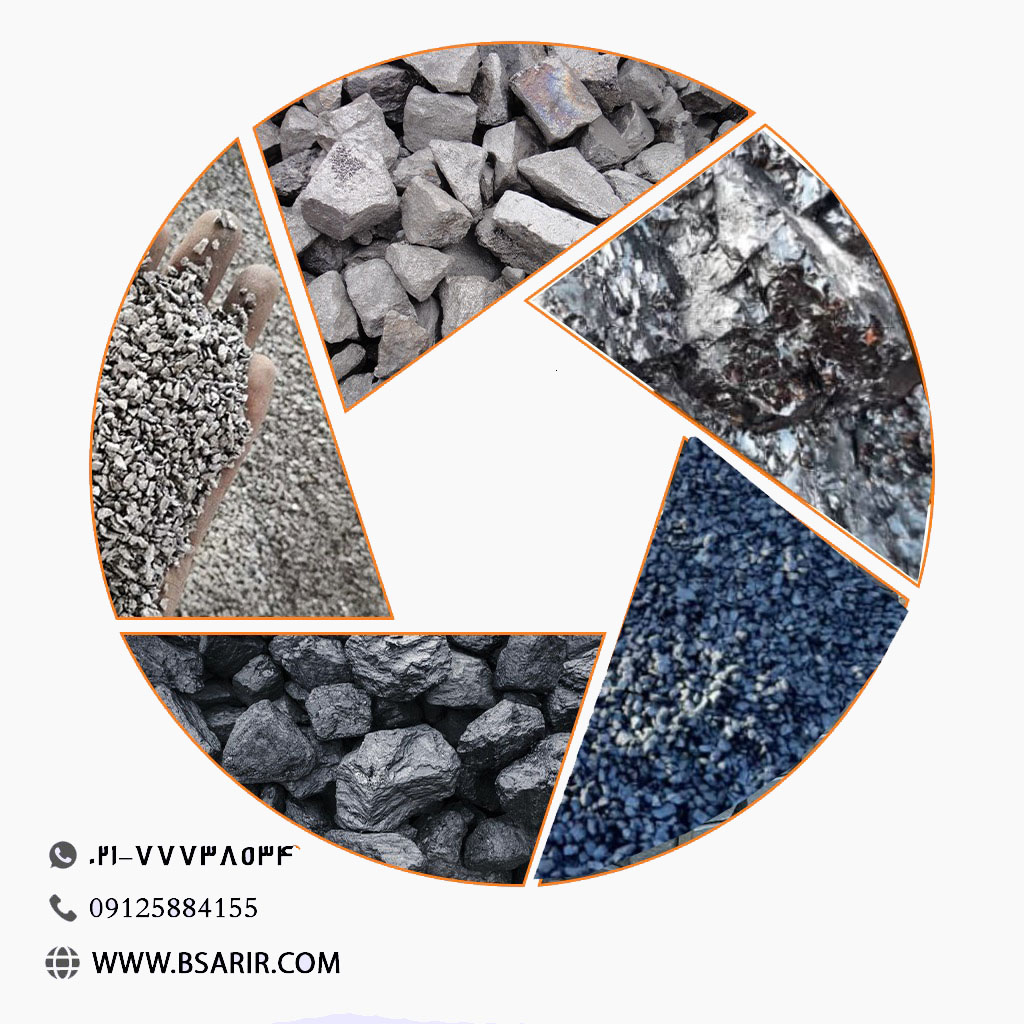
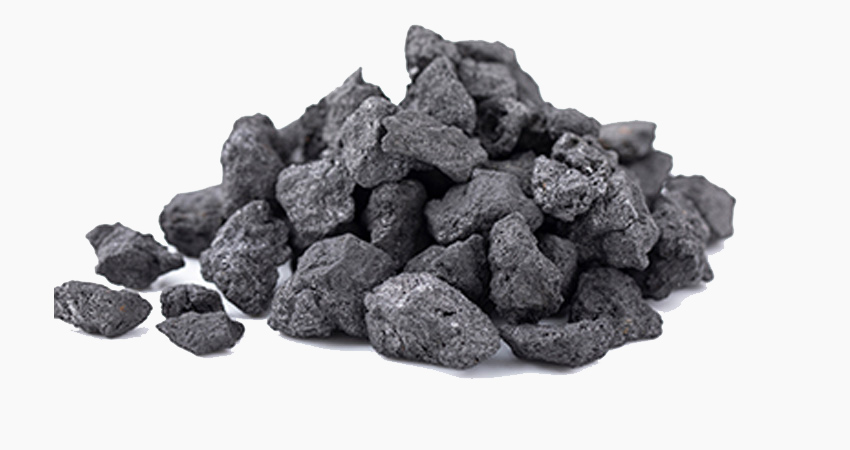
Metalurjik kokun özellikleri, fiziksel özellikler ve kimyasal özellikler olmak üzere iki kategoriye ayrılır. Bu ürünün görünümünden bahsetmek istiyorsak görünümünden bahsetmeliyiz. Aslında metalurjik kokun görünümü kömüre benzer; Ancak tek farkı parçalarının daha sert ve daha dayanıklı olmasıdır. Öte yandan çoğu durumda renkleri kristalimsi ve şeffaf siyaha benzer. Bu ürünün görünümüyle ilgili söylenebilecek bir diğer şey ise içerisinde nem bulunmamasıdır. Böylece görünüşünü gördüğünüzde bu ürünün çok kuru olduğunu göreceksiniz. Aslında bu ürün, çok küçük bir yüzde ve miktarda nem içeren saf karbondur. Kimyasal özellikleri aynı zamanda bu üründe kükürt, fosfor ve kül gibi bazı safsızlıkları da içerir. Tabii ki, yüksek kaliteli metalurjik kok, içindeki kükürt yüzdesinin birin altına ulaştığı noktaya kadar bu yabancı maddelerin yüzdesine çok düşük bir oranda sahiptir ve fosfor yüzdesi de çok küçüktür. Ancak kül ve nem yüzdesi %10-15 civarında ölçülebilir. Metalurjik koktaki karbon, kimyasal özelliklerinden biridir. Daha önce de söylediğimiz gibi bu üründeki karbonun en az %80 olması gerekiyor. Karbon, yüksek fırında metalleri eritmek için çok fazla ısı üretmekle kalmaz, aynı zamanda oksijenin demirden ayrılmasında ve demir cevherinin saflaştırılmasında da çok önemli bir rol oynar. Metalürjik kok fiyatını sorgulayabilir ve nasıl satın alacağınızı öğrenmek için bu alanda size tam anlamıyla yol gösterecek iletişim linklerinden dinamik demir satış uzmanlarıyla iletişime geçebilirsiniz.
Kok, yüksek fırında gerekli termal enerjiyi sağlamanın yanı sıra demir cevherindeki demir oksitlerin rejenerasyonunu da gerçekleştirir.Rejenerasyon doğrudan karbon (yüksek fırın formlarının önünde) veya CO2, H2 gazı ile yapılabilir.
Kolanın kalorifik değeri maksimum, nemi ise minimum olmalıdır.
Koktaki nem miktarının yüksek olması yüksek fırında uygun ısıl koşulun oluşmasını engellediğinden yüksek fırının çalışmasını olumsuz etkiler ve yüksek fırının verimi düşer.
Şu anda İsfahan'da demir eritmede kok söndürmek için ıslak yöntem veya sıcak kok üzerine soğuk su püskürtmek kullanılıyor ve kuru yöntem (inert gazla yani nitrojenle söndürme) kullanılmıyor.
بازرگانی09125884155
نظر مشتریان