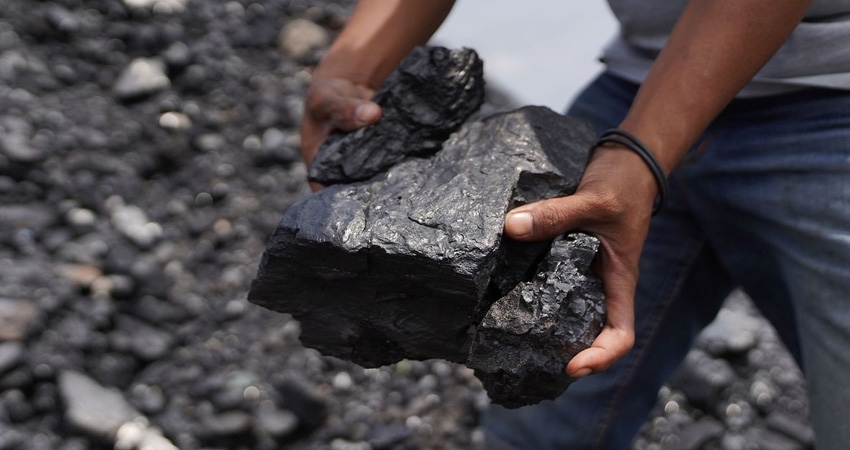
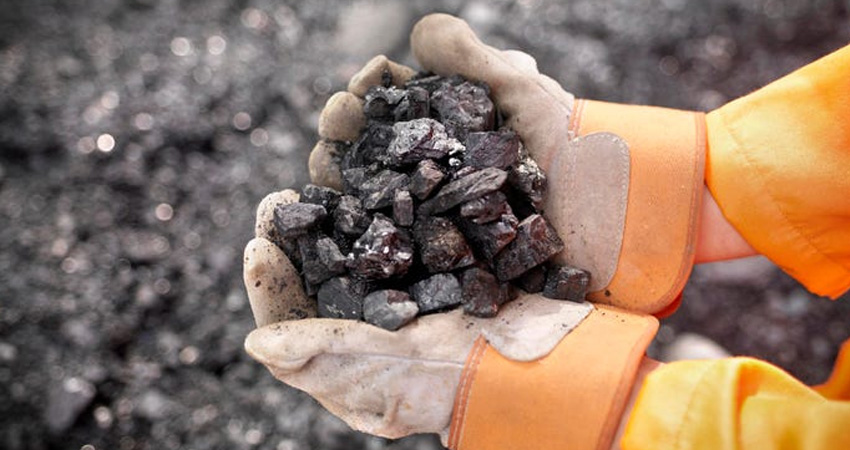
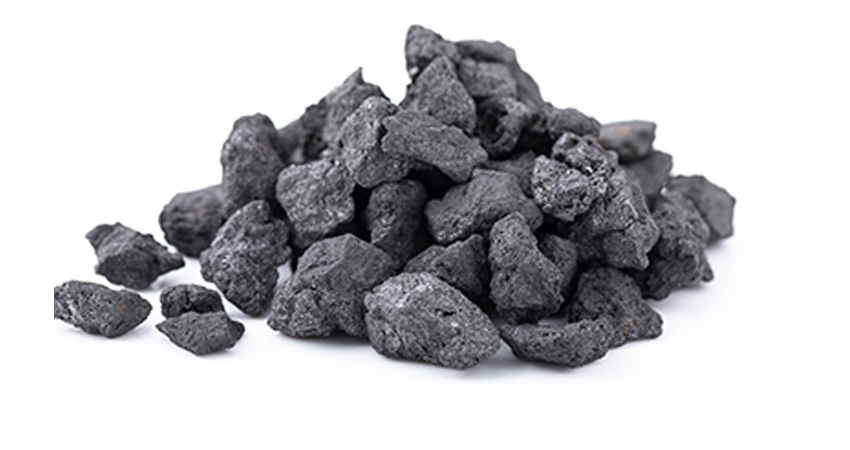
ویژگی های کک متالورژی به دو دسته ویژگی که شامل ویژگی های ظاهری، و ویژگی های شیمیایی هستند تقسیم بندی می شود. اگر در ابتدا بخواهیم در مورد ویژگی های ظاهری این محصول صحبت کنیم باید به شکل ظاهری آن اشاره کنیم. در واقع شکل ظاهری کک متالورژی همچون زغال است؛ اما با این تفاوت که تکه های آن سفت تر و مقاوم تر هستند. از طرفی در بسیاری از مواقع رنگ آن ها شبیه به سیاه کریستالی و شفاف است. نکته دیگر که در مورد خصوصیات ظاهری این محصول می توان به آن اشاره کرد عدم وجود رطوبت در آن است. بدین صورت که به هنگام مشاهده شکل ظاهری آن، شما شاهد خشکی بیش از حد این محصول خواهید بود. در واقع این محصول کربن خالص بوده که دارای درصد و مقادیر بسیار ناچیز رطوبت است. ویژگی های شیمیایی آن نیز شامل برخی ناخالصی ها همچون گوگرد، فسفر، و خاکستر در این محصول است. البته کک متالورژی مرغوب و با کیفیت دارای درصد بسیار پایینی از این ناخالصی ها می باشد، تا جایی که درصد گوگرد موجود در آن به زیر یک رسیده است و درصد فسفر آن نیز بسیار ناچیز است. اما درصد خاکستر و رطوبت آن را می تواند در حدود 10 الی 15 درصد اندازه گیری نمود. کربن موجود در کک متالورژی نیز جزو ویژگی های شیمیایی آن به شمار می آید. کربن موجود در این محصول همان طور که قبلا هم گفته ایم می بایست حداقل 80 درصد باشد. کربن نه تنها باعث ایجاد گرمای زیاد برای ذوب فلزات در کوره بلند می شود، بلکه نقش بسیار مهمی در جداسازی اکسیژن از آهن و خالص سازی سنگ آهن ایفا می کند. شما می توانید برای استعلام قیمت کک متالورژی و برای اطلاع از نحوه خرید آن، از طریق لینک های ارتباطی با کارشناسان فروش آهن پویا در تماس باشید تا شما را به صورت کامل در این زمینه راهنمایی کنند.
کک متالورژی
کک علاوه بر تامین انرژی حرارتی لازم در کوره ی بلند عمل احیا اکسیدهای آهن موجود در سنگ آهن را نیز انجام می دهد.احیا می تواند مستقیما توسط کربن(جلوی فرمهای کوره ی بلند) یا گاز CO2,H2 انجام شود.
ارزش حرارتی کک باید حداکثر و رطوبت آن باید حداقل باشد.(مقدار رطوبت کک بستگی به مدت زمان توقف در برجهای خاموش کننده و نیز مقدار جذب آب در کک دارد.)
اگر مقدار رطوبت کک زیاد باشد اثر منفی روی کار کوره ی بلند دارد زیرا از به وجود آمدن یک وضعیت مناسب حرارتی در کوره ی بلند جلوگیری می کند و راندمان کوره پایین می آید.
در حال حاضر در ذوب آهن اصفهان برای خاموش کردن کک از روش تر یا پاشیدن آب سرد روی کک های داغ استفاده می شود و از روش خشک (خاموش کردن به وسیله ی گاز بی اثر یعنی ازت) استفاده نمی شود.
نظر مشتریان